Improving aspects that may deteriorate the quality and productivity of small and micro-scale enterprises (SMEs), as well as optimizing processes that may affect the quality and productivity of companies, and ensuring compliance with technical and regulatory standards of products and services offered to the consumer. These premises were part of the axes that were developed on the project “Strengthening of SMEs in the Food Sector”, developed by the Quality and Metrology Program (Procame) of the School of Environmental Sciences of the Universidad Nacional (Edeca-UNA). For this initiative, the researchers worked with 30 micro-companies, which were given support in order to improve their competitiveness.
“We worked with SMEs from practically the whole country. The only province we did not work in was Guanacaste. The first thing we did was a calibration of the equipment; it was intended for housewives with their scales making their daily measuring tasks. This calibration is not available nationwide for micro-companies, because there are no economically viable means of metrological management to provide traceability and ensuring that the amount of raw material used, for example, is adequate”, said Karla Vetrani, the project coordinator.
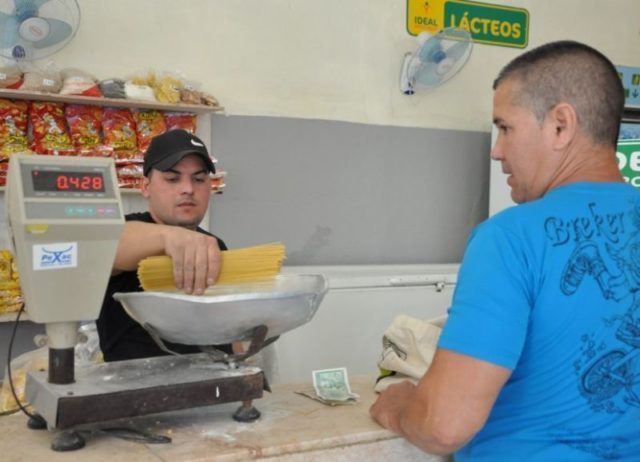
According to Ernesto Montero Sánchez, technical manager of the Metrology Lab, 11 scales, 28 thermometers, and 6 PH meters were calibrated. “There were pieces of equipment with serious errors, but it was not just calibration; we also took on the task of giving workshops to interpret the certificates and define calibration intervals. Our goal is to have technology assurance processes, where the producer may say: I calibrated this equipment; the results might serve me or not for my production process”, pointed out Montero.
Healthy environments
According to Vetrani, an evaluation of the working conditions was also carried out, applying the French LEST method, where aspects such as physical and mental loads, the environment, the psycho-labor part, and interpersonal relations, among others, are taken into account.
“Each company had at the end of the evaluation a report of strengths, opportunities, weaknesses, and threats, also known as FODA (for their initials in Spanish: Fortalezas, Oportunidades, Debilidades, and Amenazas) and we gave them some alternatives of low or no cost to make modifications. If there was a lighting problem in some cases it could be solved by moving a chair or a table, or perhaps to reduce an electrical risk, the position of the kitchen could be changed”, explained the researcher.
According to Vetrani, there is no standardization or legislation that forces micro-companies to improve occupational elements. These are a very informal sector, even though some have products placed in large supermarkets.
Preserves, pastries, bakery, chocolates, jams, “chimimurris”, juices, and ice cream were part of the products that these companies made. “We chose the food sector because it is the 2nd in growth, after the services sector. It is also a public that, although it does not have the highest educational levels, are people accustomed to working and we believe that they will take advantage of these tools for their projection”.
Impulse
By 2020, Procame expects to start a new project where, in addition to the calibration and evaluation of working conditions, the inventory of greenhouse gases (GHGs) will be included.
“We want to continue this workline with micro-companies so that they can have a new tool that allows them to join the Carbon Neutral 2.0 Program promoted by the national government”, said the researcher. For this new phase, experts intend to follow up on some of the companies that participated in the previous phase and incorporate some of the agricultural sectors.
“We want to strengthen the environmental management of SMEs through this inventory of GHG emissions and include some of the agricultural sector, especially those that produce export products so that they have an added value. Although this sector is quite complex when it comes to quantifying such emissions, our goal is to evaluate at least 16 companies, which can then enter a training phase so that they recognize the importance of not only having the inventory, by also updating it in order to maintain competitive advantages in terms of competitiveness”, she added.